MT, CVT, DC, AT transmission assembly line, with the industry's senior technical engineering team and supporting resources, with the transmission line with the whole line delivery capacity, the use of Europe and the United States Department of first-class OEM manufacturing engineering standards for customers tailored high-quality , High quality overall solution.
Including the clutch shell, the main shell sub-assembly line, the axis of the sub-assembly line, differential sub-assembly line, cover sub-assembly line, the main assembly line and test line and other parts, equipped with measuring machine, servo press, Into the box, automatic box tighten, leak test, visual inspection and other core equipment, and integrated with high intelligence MES manufacturing execution system.
The whole line adopts the world-famous KISTLER / PROMESS high-precision servo press-fit technology, the absolute value encoder feedback displacement value, high-precision piezoelectric pressure sensor feedback pressure force value, effectively ensure the accuracy of pressure to prevent thin-walled aluminum deformation;
Today's advanced and complex functions Multi-station robot working island integration technology for the input shaft assembly, output shaft assembly, differential assembly, fork shaft, tubing, etc. together and into the transmission case;
The use of photoelectric sensors, optical sensors, proximity sensors, pickup sensors, visual sensors and other intelligent sensors to determine with the PLC program, through a specific anti-error method to detect the wrong parts assembly system;
With MES and ANDON system, through the gearbox production planning distribution, material management, production file control, production information collection, the whole line running status monitoring and other functional modules, the deployment of production resources, real-time monitoring of the entire manufacturing system process material management information flow and Equipment status information flow; automatic scheduling according to the scheduling of production plans to achieve multi-species in any order mixed flow production, production process control to achieve the program, digital, remote control, assembly line equipment, intelligent fault diagnosis and alarm.
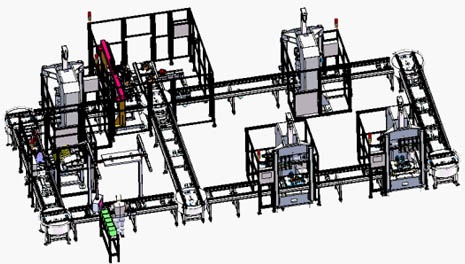
DCT gearbox shaft string assembly layout
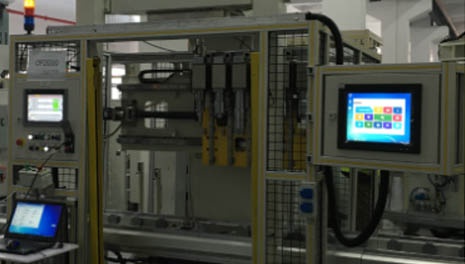
Shaft string press
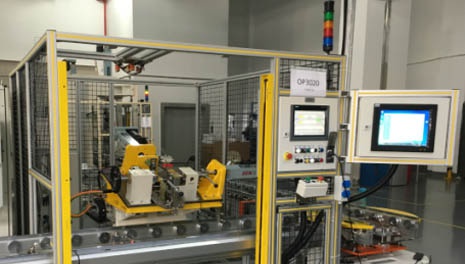
Differential assembly
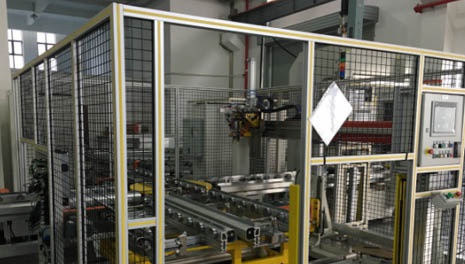
The differential is automatically assembled
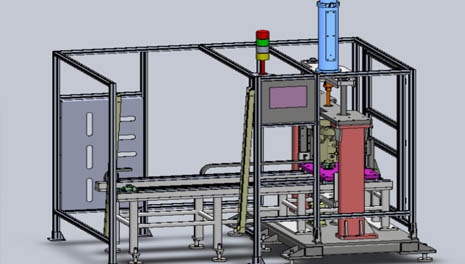
Gearbox housing bearing press fit